70% of companies that acquired logistics visibility solutions saw a return on that investment within 13 months.
The reason? Logistics visibility solutions give users, whether at the manufacturer, retailer, carrier or consumer level, access to real-time data. It seems deceptively simply, but it is not. Imagine being able to pinpoint where an order is landed at any precise second. Imagine knowing what part of the order has been processed, who processed it and what the current status is. Imagine viewing each handoff point, regardless if it is managed internally or externally, and detecting potential issues before they occur.
Let’s take a look of some of the most compelling benefits businesses take advantage of when they implement a fully integrated and open logistics visibility solution.
Seamless collaboration
Transparency and improved communications means that all stakeholders can better collaborate to increase fill rates, reduce errors in orders, prevent orders from being lost or mis-shipped, respect delivery schedules and manage delivery bottlenecks.
On-time deliveries
Guaranteeing deliveries when customers want them is critical. A logistics visibility solution can proactively identify potential risks that a delivery will not be made on time, such as supply or transportation disruptions, weather conditions or delays from upstream providers. Contingency plans can therefore be swiftly put in place to respect delivery times.
Improved inventory management
Without access to real-time information and communications, manufacturers and retailers can quickly lose their grip when it comes to effectively managing inventory.
Picture this: an order is shipped out using a third party for a customer delivery. Without the manufacturer and retailer knowing, the delivery is not made or the wrong product is delivered. The order is then sent back to the third party’s warehouse. The manufacturer and retailer have zero visibility as to where this one item is located. A logistics visibility allows companies to track any given item and any given order, regardless of the location or situation.
In addition, a logistics visibility solution can, from an operations standpoint, help to accelerate inventory management. For example, a manufacturer can position inventory at a warehouse or distribution centre that is closest to a critical mass of customers.
Respect of service line agreements
Carriers are often obliged to respect service line agreements (SLAs) to guarantee their clients on-time deliveries within large territories, adhere to delivery windows, ensure no damaged orders and respect certain levels of service quality. A logistics visibility solution provides the tools carriers need to generate comprehensive reports to prove their SLA compliance as well as survey customers to measure their satisfaction.
Increased regulatory compliance
Whether shipping items to another state or province, within a country or across international borders, a logistics visibility solution centralizes all the data and documentation required by governing authorities to clear the shipment. This, in turn, eliminates delivery delays and fines.
Reduced costs
Better planned deliveries using a logistics visibility platform can be a company’s secret weapon to reducing transportation costs, namely generated by repeated truck rolls, shipments that are not completely filled (LTL) or commingled, fraud, etc.
Simplified reverse logistics
One of the biggest profit-gouging issues in logistics and freight movement is reverse logistics—when customers receive the wrong orders, incomplete orders or damaged orders. Having to literally reverse the delivery process back upstream, either for corrective measures or proper disposal, can cause many headaches without the proper tools to carry out damage control: authorizing and tracking returns, managing inventory, overseeing material handling and routing status, dealing with carriers and contractors, the list goes on and on. A logistics visibility solution helps to ease the process for both customers and stakeholders.
Growth of a future-proofed organization
A logistics visibility solution provides in-depth reporting and analytics needed to determine and correct inefficiencies in current logistics workflows, which inevitably will reduce OPEX—but capital expenditures (CAPEX) as well. For example, gains in efficiency mean that businesses need not invest in more resources or scout out new transportation partnerships to keep their service levels in check. Furthermore, thanks to insights gleaned from a logistics visibility solution, companies can work proactively to address skyrocketing freight charges, forecast accuracy, upswings in demand and new business, evolving regulations and changes to the overall supply chain network.
In sum, all of these benefits to using a delivery logistics platform can help manufacturers, retailers and carriers increase their competitiveness and deliver on their promises for complete customer satisfaction
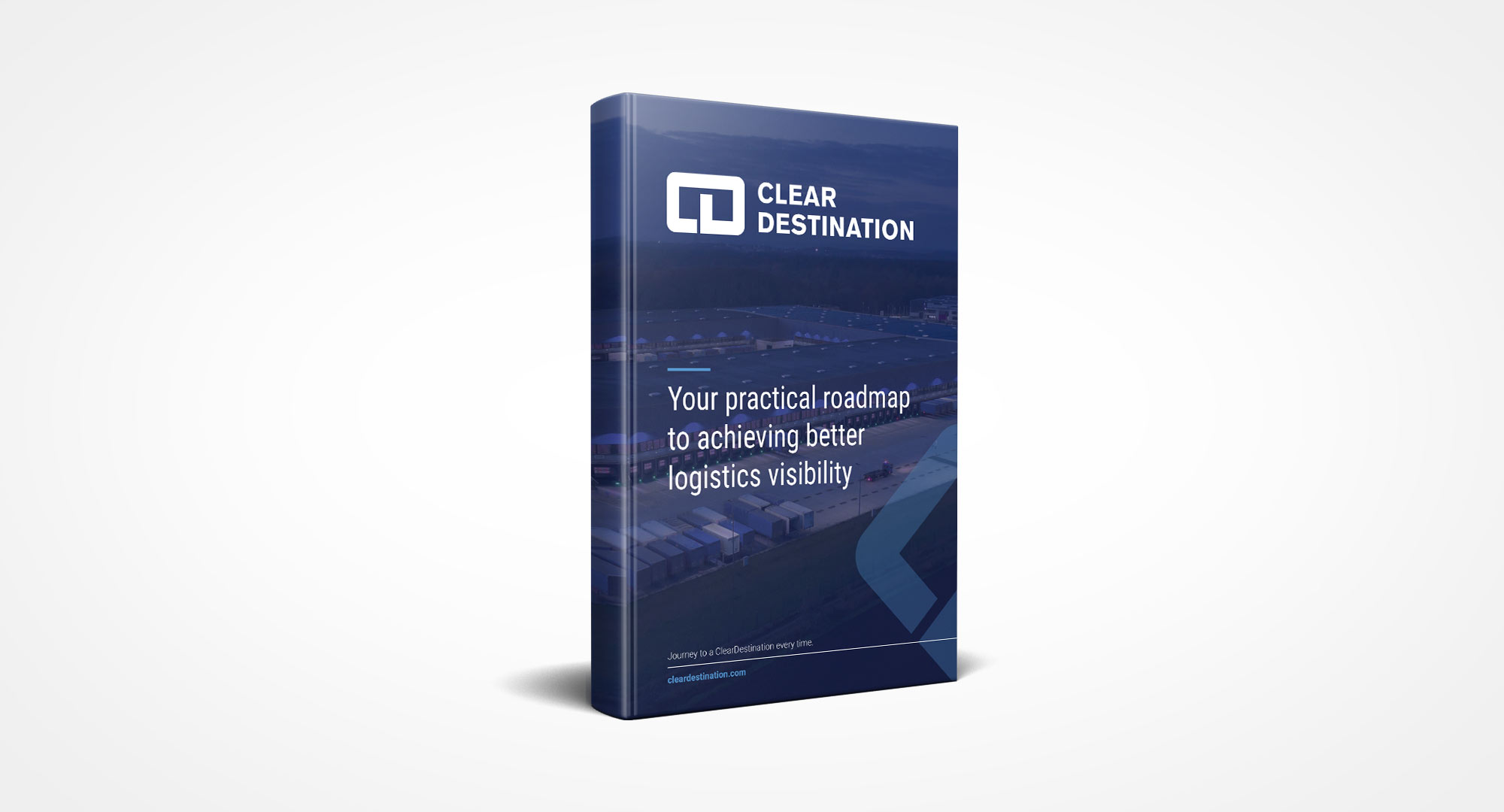
This ebook, Your Practical Roadmap to Achieving Better Logistics Visibility, provides a clear practical roadmap for forward-thinking manufacturers, retailers and carriers that are looking to achieve end-to-end logistics visibility.